On schedule to hit the water in Northern Ireland in summer 2024 is a very new type of ferry. According to developer Artemis Technologies, the EF-24 Passenger is a foiling vessel that represents a cost-effective public transportation solution to the challenges of air pollution, congestion and noise. Its design is a direct descendent of America’s Cup ‘flying’ boats but as Artemis Technologies’ technical director, Romain Ingouf, and senior naval architect, Alan Boot, explain, although that high-speed electric operation couldn’t be achieved without the foils below, it demands a rethink of just about everything else.
“The design of our hull form is very different from conventional naval architecture because we only carry that hull through the water for a very short period of time,” explains Ingouf. “When the boat starts flying, the only elements left in the water are the front and the rear foils.” As a result, volume and capacity become much more central to the design process.
The first EF-24 Passenger, planned with Condor Ferries as a Belfast Maritime Consortium project, certainly has a sleek appearance. The superstructure spans the 10.25m beam, curving into the roof and reaching forward to shelter a broad bow entry that gives 150 passengers (including cyclists and wheelchair users) easy, flat access. The central, three-crew wheelhouse is streamlined, just a few steps up from the main deck and positioned for good visibility.
However, Ingouf explains, there’s also a practical element to the flowing shape. “Once you’re foiling, the wind resistance becomes increasingly important,” he continues. “It’s an easy win for us. If you design something that is very aerodynamically efficient, you save more energy. It’s all about being attentive to such factors.” There’s an aesthetic aspect, too. The sides of the saloon are largely toughened glass, letting in large amounts of light. “We’ve all been on planes where it can feel very, very tight,” says Ingouf. “We wanted something rather different here; after all, we offer transformative technology.”
Quietly confident
That much should be apparent when the ferry starts moving. The experience on Artemis Technologies’ 12m prototype vessel suggests it will be tranquil, despite taking only 32 seconds for the EF-24 Passenger to reach its 18kts take- off point, and with only a further 20 seconds to get to its 32kts transit pace.
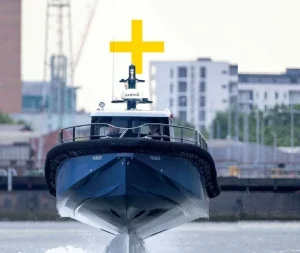
“We’ve designed and set the speed and acceleration so that it will be a gradual take-off – mostly you’ll notice the water sound on the hull just disappears,” says Boot. “You almost end up traveling in silence.” Ingouf, whose experience of foiling craft spans from his early America’s Cup days, adds, “Honestly, it’s still breathtaking.”
Some of this derives from fully electric running. The ferry has 16 tons of batteries distributed below deck, translating into 2.82MW of energy storage. That might sound generous but it’s actually considered – at least for a speed-conscious operation. “A number of electric ferries achieve a reasonable range but they’re very slow,” says Ingouf. “For a traditional build, anything over 12kts really starts ramping up the drag, reducing the range.”
So, how much does foiling actually save? “At the EF-24 Passenger’s cruising speed of between 28kts and 32kts, it uses 80-85% less energy than a traditional build,” Ingouf reveals. “It’s a game-changer.” As a result, the ferry’s batteries yield a lightship foiling range of up to 87 nautical miles: this means it can undertake several journeys without recharging. Importantly, Ingouf explains, this base design also has a longer-distance version with almost 30% more energy storage on board, enabling a 112 nautical mile lightship run. That’s certainly impressive but what is potentially more interesting is that it doesn’t take a lot to achieve this expanded capability.
“There’s room on this design to switch things around,” Ingouf explains. That ushers in a range of possibilities. Certainly, some of the world’s major cities – and remote populations – could benefit from speeded-up journey times and far lower operational costs. But there are other applications enabled by what Ingouf calls a “top hat” approach, which allows for a variety of superstructures to be fitted on this flexible base. As an example, the company has already begun to engineer an offshore wind crew transfer version.
Scaling up
Key to everything is Artemis’s in-house modular battery system, which includes thermal management and isolation strategies. “It’s a scalable solution, which means it’s possible to increase or decrease the amount of stored energy on the ferry,” says Ingouf. “That’s why it’s so important that we control the details of the vessel design – it enables us to position the weight to achieve the target center of gravity.”
However, despite the vessel system’s apparent simplicity, there have been a few power distribution issues to overcome. “If you’re using a 400V system, we’re talking about cables that are around two to three times the diameter of 800V systems,” explains Ingouf. “So, you can imagine how challenging it is to package three, six or even nine cables that size inside a vertical strut that you want to be as thin as possible – and how hard it is to simply get them around corners.”
Therefore, the main DC bus is pushing around 700-800V, giving the drivetrain 97% efficiency with lower-voltage AC spurs for house loads. This enables cabling just a few centimeters across to link with the electrical switch room at the rear of the boat. Arguably, it’s below the waterline that the magic happens: there is a very large π-shaped main foil with two struts and efficient twin motors delivering peak power of 650-700kW. That’s another bespoke, in-house Artemis solution because, says Ingouf, a motor with that voltage, moving at speed, 3m below the surface needs rigorous testing and production – in short, the teams wanted to make sure the motor was up to the job.
And these do have a large job to do: the main foil’s wingspan is around 10m – about as big as possible without interfering with alongside docking or other operations. However, it isn’t placed near the bow as some might expect. As this foil generates most of the lift, Ingouf explains, it’s positioned as close to the boat’s center of gravity as possible, rather like an aircraft wing. The aft, T-shaped foil helps control pitch and roll motion when foiling, and during low-speed displacement maneuvers it also behaves as a rudder.
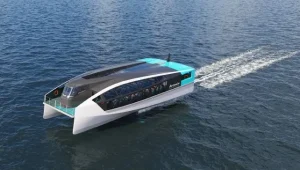
Importantly, these aren’t retractable foils, although this is offered as an option. “We wanted to offer a base design that is as efficient as it can be,” says Ingouf. This meant it was important to avoid extra cost, complexity and weight issues. The knock-on effect of this choice, however, demanded an exacting analysis of draft requirements. To that end, the company took on an in-depth study of typical passenger ferry operations which, in turn, informed several parameters.
“We actually made the shape of the hulls as shallow as possible – while maintaining necessary volume – as that maximizes the vertical span of the foils from the bottom of the hull,” says Ingouf. The boat has around a 3m draft in all, which, Ingouf explains, “allows you to fly as high as you can while still enabling access to most harbors”. Hitting that design sweet spot, he continues, also means the struts are deep enough to allow a trade-off between bringing the hull out of the reach of the waves and propeller immersion.
“You need the foils to be under enough water so the propellers don’t catch the air or ventilate and lose efficiency while flying.” There’s good reason for Ingouf’s use of the term ‘flying’. Much of the physics is similar, in principle. In fact, foiling depends on an active flight control system that operates rather like that of an aircraft, with aileron-like flaps on the main and rear foils. Turning is achieved by using these to induce the right amount of heel, and Ingouf describes how “the moment you start moving the wheel, the vessel starts to bank – a bit like a motorbike”.
But while this sounds straightforward, the system operates in six degrees of motion and there will likely be sensor data to incorporate. It also has a useful effect on the ride. “We use that same flight control software in our simulation world so that we can put the boat through different conditions, waves from the side, 3m in height, and so on. That allows us to observe and post-process things like efficiency or passenger comfort through an acceleration matrix,” says Ingouf. As a result, the flight controller can swap between modes to find not only the most efficient way to perform the journey but also the most comfortable. While the hull is usually foiling around 1m above sea level, “some days you’ve got choppy waves, which might mean you want to fly a bit lower”, he adds.
“Even when we were in the America’s Cup team, we didn’t have this capability – we just created that over the last
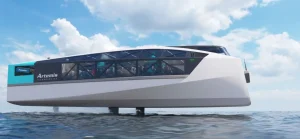
couple of years,” Ingouf says. “It’s unique.” And because the vessel does, kind of, fly, it’s important to ask the question – what if it crashes? The Artemis team underlines that, first, the company’s eFoiler propulsion system has a high level of redundancy: key sensors feeding the flight controller have spares working in parallel, just in case of failure (such as IMU or ride height). In addition, these designs have been subject to thorough simulation analysis, with all load cases having more than met the regulatory requirements. And of course, to keep things in perspective, there’s also a hull beneath and, in contrast to an aircraft, the EF-24 Passenger only flies a couple of meters above the waves, so it has a much softer landing. The first Artemis EF-24 Passenger ferry, set to launch this year, will be operated by Condor Ferries and service a route between Belfast and Bangor in Northern Ireland.