Yamaha is working with Roush Industries and Regulator Marine to evaluate the adoption of hydrogen fuel in an outboard engine application.
Back in July 2024, a team from Roush Industries and Yamaha Motor Corporation loaded a specially adapted Regulator Marine hull onto a transporter. They took it to a hydrogen fueling station in Flint, Michigan, to fill the storage tanks of the 8m vessel – powered by the world’s first hydrogencombustion outboard motor – for the first time.
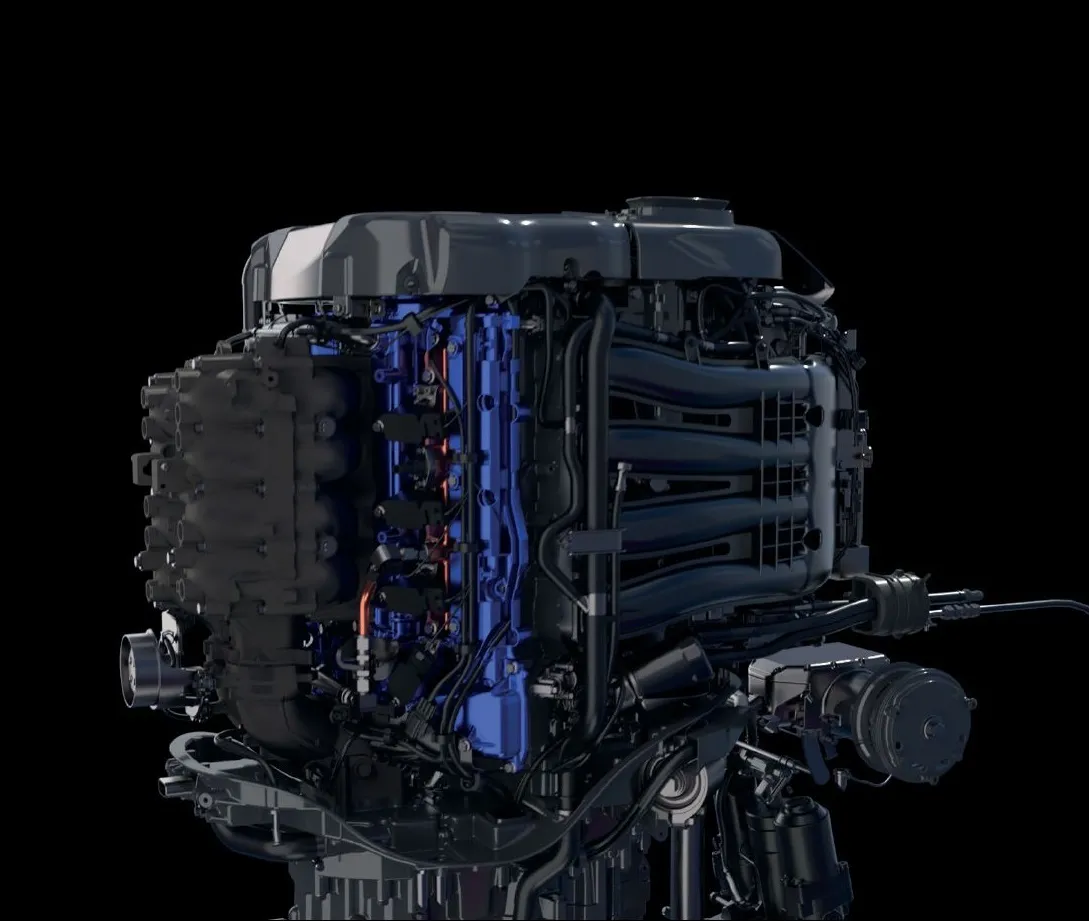
“It was a big moment,” says Matt Van Benschoten, vice president of advanced engineering at Roush, a company with long experience with hydrogen fuel systems and engaged by Yamaha as the fuel systems integrator for the project. Roush was responsible for systems design, specifications development, physical integration, safety system analysis, and testing and development.
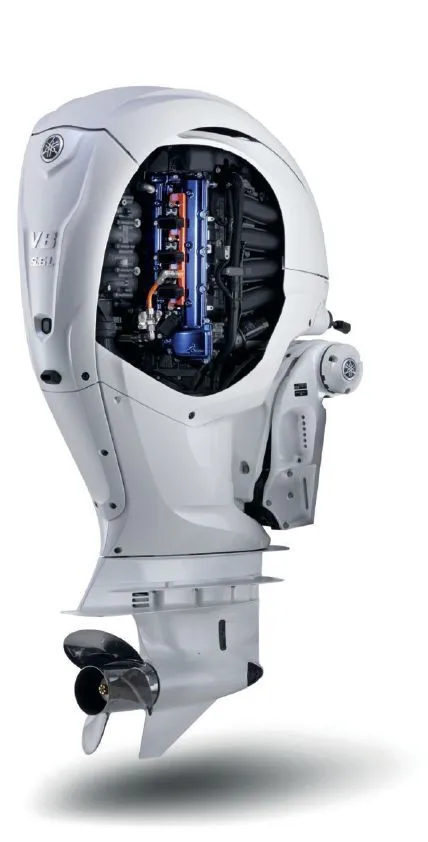
Yamaha has been working on a marine application of gaseous hydrogen-combustion technology for the past couple of years as part of its multitechnology approach to carbonneutral products, which includes sustainable drop-in fuels, electric applications and alternative fuels such as hydrogen.
“Successfully applying hydrogen-combustion technology to a marine application has only been possible because Yamaha has multiple product divisions, including motorcycles and automotive,” says Dr Grant Suzuki, the company’s chief of technology for marine innovation engineering at the US technical center in Kennesaw, Georgia. “We’ve been doing advanced development on a hydrogen-combustion engine on the automotive side for a while, so we can leverage that experience across the product portfolio. Earlier this year, for example, we also demonstrated Drive H2, a prototype hydrogen-combustion golf cart.”
Demonstrator package
Yamaha’s hydrogen-combustion outboard engine, first revealed in Miami in February 2024, is based on the 450hp XTO – the company’s largest offshore outboard. It has converted the powerhead by tweaking mechanical designs, changing materials and replacing components as needed in areas such as the cylinder heads, fuel lines, inlet and injectors (the XTO has direct injection) to accommodate the characteristics of the hydrogen fuel. Most other components are the same as in the standard, gasoline-fueled outboard. Yamaha is cagey on the exact changes being made but says that engineering work has now moved into an optimization phase.
The test hull, based on a Regulator Marine 26XO pleasure fishing boat that’s normally powered by a gasoline XTO 450, has been modified with a bespoke H2 storage and delivery system designed by Roush. There are three 700-bar Hexagon Purus storage tanks and four pressure reducers connected by a network of stainless-steel fuel-delivery pipes. As fuel enters through the single inlet on the port side, it runs to a central, high-pressure manifold, from where it splits to fill the three tanks.
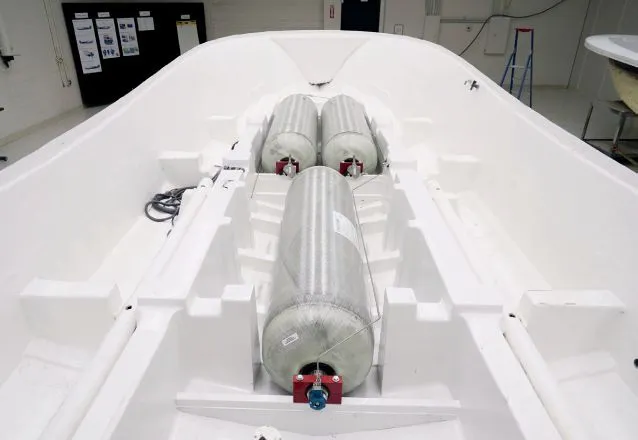
“Successfully applying hydrogen-combustion technology to a marine application has only been possible because Yamaha has multiple divisions, including motorcycles and automotive”
Dr Grant Suzuki, Yamaha
“The tanks expand as they fill,” explains Yamaha marine advanced development engineer Kassidy Peterson. “We had to design the mounting in such a way that at the manifold, the tanks are solid and the connections are very secure. But at the far end of each tank, it can slide. There is space for it to move as it expands lengthwise, as well as around the tank for it to expand radially.”
The vessel has a standard SAE J2600 refueling connector for gaseous hydrogen and the J2601 fill-rate protocol is followed. An IR wireless connection between the boat and the fill station communicates tank and vessel information so that the correct charge rate is used. It shuts down the refueling process if the temperature limit on the tank materials – typically 85°C – is reached.
“The tanks expand as they fill. We had to design the mounting in such a way that at the manifold, the tanks are solid and the connections are very secure. But at the far end of each tank, it can slide“
Kassidy Peterson, Yamaha
A step-down pressure regulator reduces the hydrogen’s pressure to 100 bar for delivery to the engine. Roush’s Van Benschoten notes that the inability to use anything from atmospheric pressure to 100 bar limits the usable capacity of the tanks and therefore affects the boat’s range.
The 720 liter total capacity of the three cylindrical tanks was determined by a desire to fit as much fuel as possible into the existing shape of the hull. At 700 bar, the onboard hydrogen fuel is roughly equivalent to 23-24 gallons of gasoline – just short of 25% of the capacity in the 26XO’s normal, 107-gallon gas tank.
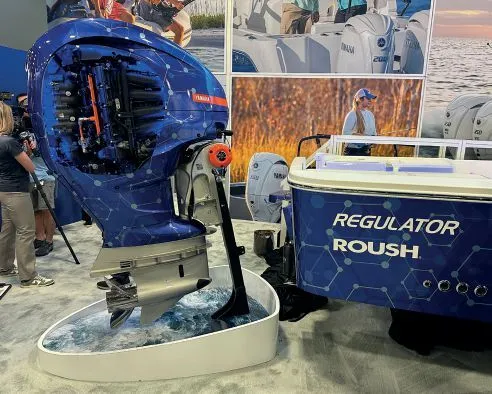
“One thing to consider for the future would be conformal tanks that package better within the hull space, so we don’t have to scar the vessel so much,” says Van Benschoten. “Regulator has been an excellent partner in this program. When we told them we wanted to cut away some of the bulkheads, they didn’t panic! They said, ‘Let us think about how we’re going to accommodate that.’”
He adds that finding components for a 700-bar gaseous hydrogen fuel system was not as straightforward as it might have been for the more widely used 350-bar standard. “The supply base is less mature. We spent a lot of time identifying tanks, regulators and solenoid valves. We were concerned not only about the explosion aspect – making sure those components are electronically sealed – but also that they’re suitable for a marine environment.”
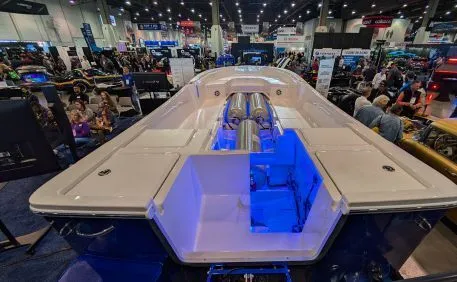
Safety strategy and testing
Roush also designed a ventilation system for the hull. The Type 4 tanks have a defined, very low permeation rate but they leak all the same. With hydrogen, ventilation is from the highest points of the vessel, as opposed to the usual practice of venting an inboard engine’s gasoline vapors from the bottom of the hull.
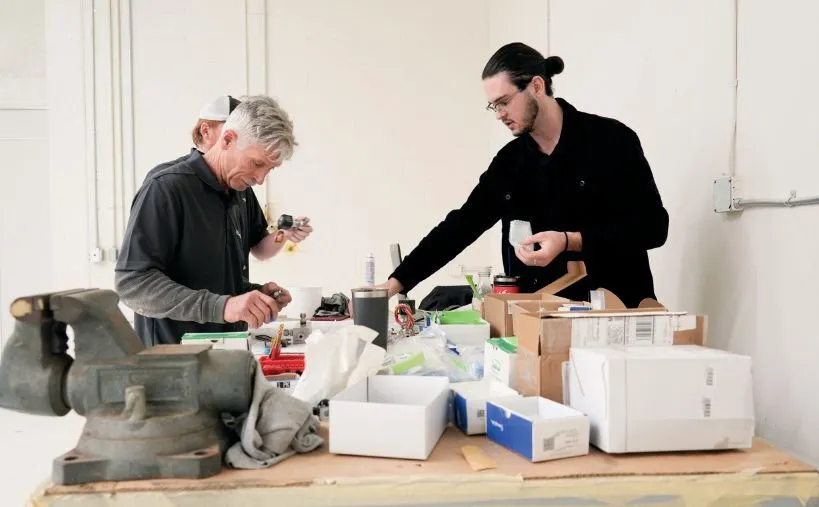
Five hydrogen detectors are mounted high where the hydrogen will collect, feeding back to a supervisory controller as part of a Roush-developed control and safety system. If any of them sees a 1% concentration of hydrogen, it notifies the captain via the HMI. If the concentration hits 2%, the vessel shuts down and vents the fuel system.
“The next step will be running through the entire design validation plan (DVP), making sure that the response we’re expecting to a particular failure mode occurs,” says Van Benschoten. “The Regulator team is also interested in the performance of the boat from a center of gravity perspective. We moved the CG forward quite a bit and we haven’t ballasted it, but the demo boat still floats quite well. Then it’s about evaluating the performance of the boat – what sort of range are we getting from it, for example.”
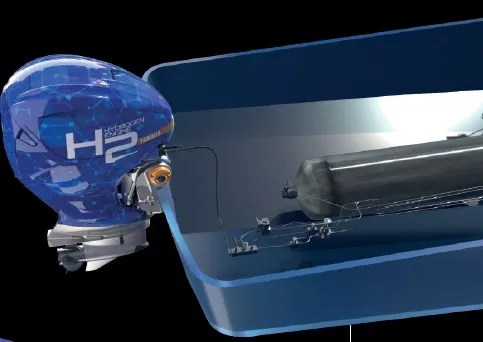
Another part of executing the DVP will be to establish the real-world fill rate: theoretically six minutes but likely to be closer to 10. At the time of writing, the team had yet to do a regular refuel from 100 to 700 bar, having had to purge inert gas from the tanks during the initial fuel-up in Flint.
This article was originally published in the January 2025 issue of Electric and Hybrid Marine Technology. To view the magazine in full, click here.