Electric offshore support vessel operations cannot rely on portside battery top-ups alone, which means there are opportunities for on-site charging at offshore wind farms. However, this change of environment brings its own set of considerations and challenges.
Fast-charging infrastructure is being rolled out at harbors and ports across Europe, but there’s a problem: a shoreside charge only carries you so far.
In the offshore renewables sector, it has become obvious that the ability to efficiently operate fully and partially electric CTVs (crew transfer vessels, tasked with shuttling offshore wind turbine technicians between shore and site) and larger SOVs (service operation vessels, which accommodate these personnel on-site for extended periods) depends on the availability of offshore charging points.
Dimitri de Gunzburg, charging systems development lead at Charge Offshore, points out that, “Vessel owners need to decarbonize or else they will have to pay carbon credit compensation under forthcoming EU regulations. Economically, it doesn’t make sense to operate fully on diesel anymore.” However, a single harbor charge is insufficient to power a CTV’s working day, which typically lasts 9 to 12 hours.
Meanwhile, for SOVs parked on-site for two to three weeks at a time, “A single harbor charge is not even an option,” de Gunzburg adds. “Both vessel types require offshore charging unless they opt for hydrogen or methanol as a stand-in fuel. A lot of ferries in Norway have been running on batteries for years, so the class societies are used to the challenges and constraints of installing batteries on a boat – but this isn’t the case for hydrogen.” As a result, offshore charging will become “mandatory for zero-emission operations”, de Gunzburg explains.
“The industry is moving toward offshore charging, gradually. But first, people want proof of concept.”
Dimitri de Gunzburg, Charge Offshore
Support network
Consequently, Charge Offshore – a venture established by maritime charging solutions provider MJR Power & Automation, mechanical engineer Blackfish Engineering, CTV operator Tidal Transit and software engineer Elsys – has launched its Aquarius range of offshore charging systems for pure and hybrid electric wind farm support vessels. The range includes the Aquarius Eco, designed to provide 0.5-2MW of power to CTVs, and the Aquarius Plus, which can deliver 2-8MW of wind-captured energy to larger SOVs, directly from offshore turbine parks.
This charging tech has been put through its paces. In harbor trials in the UK in 2023, it was used to charge a 20m Tidal Transit CTV, Tia Elizabeth; in a Parkwind offshore wind farm demo, hosted in July 2024, it was tested with multiple connections and live power transfers to a CTV.
Still, there are hurdles to overcome before these charging points can be established at offshore wind farms or on offshore structures.
“The main challenge is the structure’s ability to provide suitable charge power to the charge unit,” says de Gunzburg. “It is relatively straightforward when integration of the charge power supply is considered at the structure’s design stage, but more challenging to retrofit this onto existing infrastructure.” The Aquarius chargers can be installed directly onto the substation, a dedicated monopile or “anything that sticks out of the water”, he says.
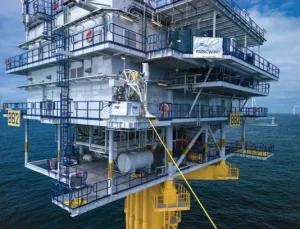
Charging process
The safety issues related to marine cabling are well known. This equipment is used extensively to power seabed trenchers and remotely operated vehicles, de Gunzburg points out. As such, it is already subject to stringent offshore safety requirements, such as HAZID/FMECA reviews at the design stage. “The system is built from proven marine-grade components, which have gone through rigorous qualification programs, witnessed by [classification society] DNV,” de Gunzburg says.
The Aquarius chargers are designed for hands-free connection, with the process managed from a console on the bridge. The vessel approaches the tower – CTVs pushing onto the boat landing, SOVs remaining at a distance of 10-12m – and then an automated reel on the structure lowers a connector into a receptacle aboard the vessel.
“The CTV then moves away from the structure to a safe distance and weathervanes to hold position, while the SOV stays on loose dynamic positioning, at a distance of 50-80m from the structure,” says de Gunzburg. Based on simulations conducted with various ship operators and designers, charging times should amount to one to two hours for CTVs and two to four hours for SOVs.
“We have standardized the charger so it can charge both CTVs and SOVs,” de Gunzburg adds. “The only difference is the power input: above 4MW, it’s just the connector and cable that change to a higher voltage. CTVs don’t typically carry more than 3-4MW of batteries on board, so a 2MW charge is more than enough. The bigger the charger, the bigger the power converters you would need on the CTV, and that would compromise the payload capability.”
Charge Offshore has already sold its first commercial Aquarius unit, rated 1.2MW, to an unnamed client, and this piece of kit is expected to become active in the field in Q3 2025. The group also expects to supply Aquarius chargers to future Damen new-builds and to eight fully electric CTVs under construction for Tidal Transit.
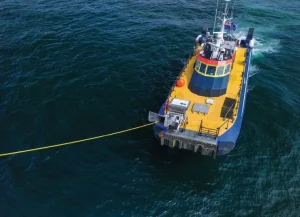
“The industry is moving toward offshore charging, gradually,” says de Gunzburg. “But first, people want to explore proof of concept – maybe for six months or a year – to build up their confidence in the technology. Once they have this confidence, I think the offshore charging market will expand quite fast.”
Orkney demo
For Nigel Robinson, offshore renewables director at engineering firm Apollo, it was CTV/SOV operations in Scotland and the North Sea that convinced him of the need to offer additional chargepoints outside of the ports.
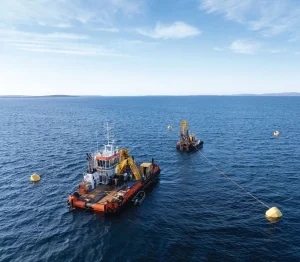
“There is a physical limit to how much you can charge,” he says. “To reach some of the farther-out Scottish offshore wind developments on electric power is an awfully long journey for a CTV; you need a way of doubling your range.”
“These wet mates are designed for depths of 3,000m – well over-specified, considering the worst the charger will experience is a dunking and maybe a bit of spray.”
Nigel Robinson, Apollo Nigel
Prior to 2024, Apollo had been fine-tuning its Palm Quick Connection System (QCS), originally designed for subsea cables for offshore renewable structures.
“During the testing, with the Palm QCS all rigged up in a big frame, we thought, ‘This could work as a charging point for offshore vessels,’” Robinson recalls. Having secured funding from Innovate UK’s Clean Maritime Demonstration Competition in Q1 2024, Apollo teamed up with the European Marine Energy Centre (EMEC) and Orkney contractor Leask Marine to assess the viability of adapting the Palm QCS for this purpose.
The partners split the project into two parts: first, a mechanical proof of concept, to be validated in an offshore environment; and then a commercialization study to assess the best way to roll out the charging solution to the industry. The resulting solution, now called the Palm Charger, was tested at Scapa Flow in the Orkney Islands.
One of the first considerations was where to position the charging system. “From conversations we’ve held with stakeholders, we’d probably mount the Palm QCS on the offshore substation, taking power directly from there as opposed to routing it through a turbine,” says Robinson. “It could, in principle, hang off the transition piece, but the substation offers a more direct source of charge.
“Space on the substation is at a premium, so we’d maybe factor in a deck extension on the substation – we’re still working that part out. It’s a challenge but it’s not insurmountable. We imagine having two connectors at a wind farm, to enable connections on either side of the prevailing weather.” Robinson adds that this decision would also largely depend on who owns the substation: “There are differences between the ownership of the substation, depending on which regulatory regime applies, so the model for the UK may differ from that for Germany, for instance,” he says.
Load monitoring tests
For the trial, Leask Marine contributed its 27.3m multi-cat C-Force; not an electric vessel, but kitted out to mimic an offshore wind farm support craft.
“We didn’t physically charge, but instead demonstrated the connection concept through load monitoring,” says Robinson. The vessel was equipped with a power interface, a cable reel and the Palm Charger plug, which was used to connect the vessel to the charging point.
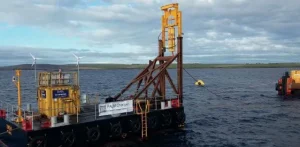
A prototype, low-voltage version of the Palm Charger was patched into a frame representing the substation and gimballed off the top, so that it hung from the top of the structure – “in a good place for a boat to come along and grab hold of the messenger line”, according to Robinson. The vessel hooked up the plug and winch to a work wire and then used a winch to wind the plug into the receptacle, establishing the connection. The winch wire was then pulled to release the system and bring the connections back to the boat.
“We completed 30 successful disconnect/reconnect ops in the field,” says Robinson. “We had some last-minute setbacks to overcome, and the weather wasn’t always friendly. We started off with a connection time of four to five minutes but got this down to two minutes through suggestions from the vessel’s crew.” Charging would be weather-restricted to prevent excess vessel motions, although, Robinson adds, most offshore vessels would presumably work off some form of dynamic positioning “within a watch circle”.
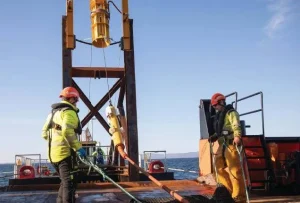
Regarding safety, the Palm Charger incorporates marinized wet mates. “These wet mates are designed for depths of 3,000m – well over-specified, considering the worst the charger will experience is a dunking and maybe a bit of spray,” says Robinson. “Other than that, the system incorporates steelwork, so you’d apply coatings and perhaps cathodic protection to protect it from the offshore environment.” This core knowledge is not without precedent: “We’re using expertise that’s been cultivated through oil and gas – for example, DP, riser and hose transfer operations, and so on,” he explains.
Power options
In terms of power, the jury is still out on whether an 11kV charge or a 66kV charge is required: the former would probably require a step-down transformer and extra equipment at the substation, while the latter would put the transformer on the vessel side.
According to Robinson, “11kV suits the vessels well, while 66V suits the platforms well. There’s also the issue that some developers aren’t sure who’s going to carry the burden of getting this fixed up. Is it the developer who provides the facility for the vessel to charge up? Or does the developer say to the vessel operators, ‘You have to provide the equipment for us to adopt into the structure’?
“We’re looking at a required power range of around 5MW for SOVs – it’s hefty stuff,” he continues. “Future studies will have to assess how you run all that power through quite constrained areas; the optimal size for the different cables; and the thermal effects between the different cables. The industry also needs to look at certification and insurance.”
According to Robinson, the ideal next step for Apollo would be to launch a pilot deployment with a fully functioning Palm Charger and an electric offshore support vessel.
Enabling E-CTVs
As offshore charging technology evolves, so does the viability of a wide-scale electric offshore support fleet. Last year, Dutch shipbuilder and naval architect Damen introduced its 7017 E SOV concept: a 4,300gt SOV designed to house offshore technicians and crew across 60 single cabins. In trials, the 70 x 17m vessel used its motion-compensated gangway (typically used by offshore technicians to access the wind turbines, or carry equipment from ship to site) to create the connection between the vessel and the substation.
Further electric CTV development is on the cards: Charge Offshore’s de Gunzburg says his company is talking to a Norwegian shipyard keen to develop electric offshore vessels, though he declined to reveal their identity. However, the evolution of offshore charging will rely on a coordinated effort from industry. As Damen put it last year: “To make this a reality will require collaboration throughout the chain, with the shipbuilder, the vessel operator and the wind farm developer working together in pursuit of mutual benefit.”