With much thought given to propulsion system design, the area where the power meets the water can often be overlooked. E&H Marine explores some of the subtleties of propeller design that can affect electric and hybrid vessel efficiency.
Developers of electric and hybrid propulsion systems often (justifiably) shout about their efficiencies and make valid comparisons to old-school internal combustion engines.
One of the most exciting aspects of the marine sector’s fast-moving transition to electrification is the renewed focus on anything that can be done better than before. Pioneers are super keen to embrace and integrate technology that enhances efficiency and improves the user experience.
In motorsport, there is a continuing fascination with tire choice – where vehicle power is put to the tarmac. But has the electric and hybrid marine propulsion industry overlooked the space where all its 21st-century smart technology interacts with the water?
The subject of propellers comes up in every electric or hybrid vessel project. In most commercially available off-the-shelf products, stock propellers are designed around an ICE’s performance statistics – so a project will inherit open hubs, ventilation ports, specific sizes and designs that work with those ICEs. But these options are not always optimal for the characteristics of an electric drive.
These characteristics are different in that the drives provide torque at RPMs that ICEs can only dream of. This enables consideration of propeller sizes that would normally prevent an ICE from producing the required RPM and torque required for the vessel.
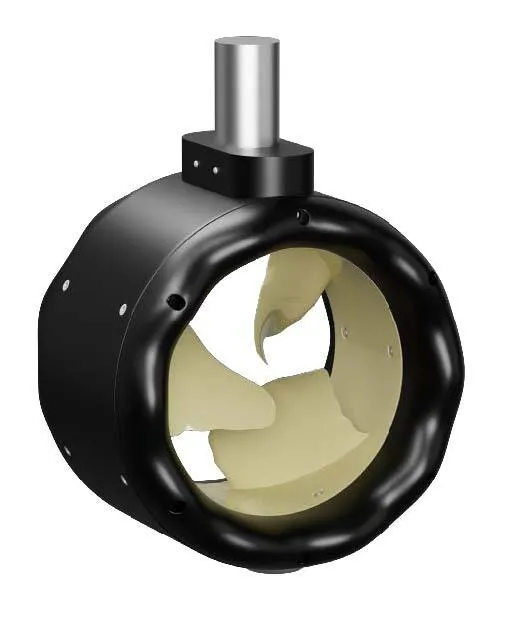
Finishing strong
Fouling of hulls is a huge topic, with the coatings industry providing solutions that protect assets and try to keep a hull’s efficiency as close to the day it first touched the water. But it seems that only the largest shipping companies address propeller surface roughness – with factors such as use profile and fuel costs driving a need to focus on a propeller’s surface finish.
Vessel owners and operators invest in maintenance of the underwater hull surfaces, including the propellers, but for many sub-24m vessels, consideration of propeller surface finish is rare. However, this is an area where there are clear gains to be made – and evidence to back up the science.
Hempel’s Ecopower and Silic One are created specifically as coatings for propellers and hulls. As the company’s product manager, Chris Toole, explains, “The Ecopower product, and especially our premium Silic One product, prevent fouling build-up on the propellers, making the prop function more effectively with less weight on, compared with uncoated propellers.” He goes on to emphasize “the importance of coating the propeller instead of leaving it uncoated”.
David Sheppard, a manager at Bruntons Propellers, says, “The smoothest surfaces generally give the best performance, but anything that is considered hydraulically smooth will give similar performance.”
The ISO standard for propeller surfaces has a limit of 2 microns Ra for Class S propellers and 3 microns Ra (from 30% of radius out) for Class I. There have been experiments using special surface treatments, such as coatings, riblets and dimples (similar to those on a golf ball), but none of these have been shown to provide a significant performance increase compared with a smooth surface.
As propeller coatings and enhanced surface finishes are an investment, it is important to understand what level of efficiency gains might be expected.
As Sheppard explains, this depends on several factors, including propeller loading, blade area and the operational profile of the vessel. For example, in the case of a merchant ship propeller, gains can be higher for a high-speed vessel. But it depends on how rough the comparison propeller is before cleaning. In addition, it is more productive to keep the outer half of the blades smooth rather than the inner half, due to the higher rotational speeds of the outer sections.
Surprisingly, Sheppard explains that Bruntons rarely receives requests for surface finishes higher than that of ISO Class I or S, which come as standard from most propeller suppliers.
According to Sheppard, surface finish is considered to be relative to efficiency. It is more well known – and more widely discussed – in academia and within the propeller design community than among customers and end users. For many end users, propellers are typically only cleaned on a semi-regular basis or if boats are stationary for extended periods.
“[Our solutions are] designed to integrate seamlessly with major drive systems“
Alois Bauer,
Hydro Impulse
Optimized for electric
US-based propeller specialist Sharrow Marine is making waves in the electrification sphere. Founder and CEO Greg Sharrow explains that commercially available off-the-shelf propeller designs that are optimized for gasoline and diesel motors are not equally optimal for electric motors.
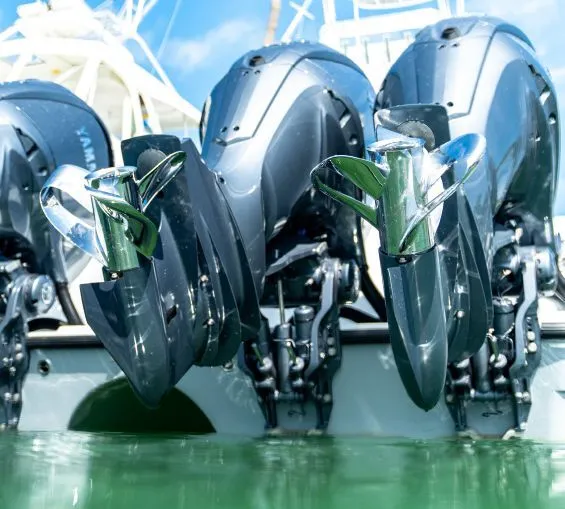
This highlights, again, the importance of specifying the propeller for the application – and not trusting that the best, proven propeller options for legacy drives are always the smartest choice for electrified propulsion.
Smart imitating life
Cycloidal propulsors’ bladed movement, bionic propellers and tubercle technology all have their origins in biomimicry. Piggybacking on evolution is nothing new, and opting for a design that has been refined, in the field, over millions of years seems like a no-brainer.
Drive manufacturer BlueNav is seeing the benefits gained from integrating biomimicry into its drive design and the interaction between its technology and the water.
“BlueNav embodies the sophistication of nature’s influence, and has been inspired by the graceful dynamics of whales,” explains company co-founder and CTO Hervé Frouin. “Our engineers found inspiration in the wonders of nature, particularly the unique features of humpback whale fins. These fins have special serrations (tubercles) that are believed to control water flow. Our engineers used this idea to design blades and a nozzle that are different from the usual.”
The streamlines from the blades’ crests suggest better flow behavior around the troughs. This change in pressure and speed downstream of the propeller blades means an increase in thrust, leading to a substantial boost in propeller power. The nozzle has an asymmetrical design at the inlet and outlet, helping the boat move forward. Materials and surface conditions have been optimized to copy the low friction observed in whales, ensuring sliding performance.
Impulse control
For applications that apply a high thrust loading at the propeller, significant gains in performance can be made by enclosing that propeller in a duct. Ducted propellers are typically good for high-thrust applications and are commonly seen on tugs. But because the nozzle creates drag, high-speed vessel applications have not proved to be successful in the past. Times are clearly changing, however, and further research and testing is bringing solutions to market.
Hydro Impulse manufactures cutting-edge impeller solutions, designed as a result of three years of development. Alois Bauer, managing partner at Hydro Impulse, explains that the company’s solution is “designed to integrate seamlessly with major drive systems, including outboards, stern drives, pod drives and shaft drives, offering double-digit improvements in efficiency”. The Hydro Impulse solution picked up the E&H Marine Environmental Achievement of the Year – Propulsion System Design award in 2023.
“The Sharrow propeller utilizes its patented twisted and curved blade shape designed to reduce drag and turbulence in the water”
Greg Sharrow,
Sharrow Marine
Bauer goes on to explain that users can expect at least a 15% reduction in energy consumption. Furthermore, the company’s latest product, the HI-RF 11 Mitek, demonstrates significant performance enhancements in the Mitek MO 15 outboard. Compared with conventional propellers, it provides up to 30% more thrust than thrust-oriented propellers and 60% more thrust than speed-oriented propellers. These improvements not only reduce energy consumption but also deliver comparable performance more cost-effectively than higher-powered systems.
Clear waters
The advantage of clear water flow forward of a propeller is obvious, but the science of what happens to this flow as it is impacted by the rotating propeller is vital because this affects propeller efficiency and noise. A hub vortex, created behind a propeller, has a negative effect on propeller performance, and manipulating the post-propeller flow is another science altogether – albeit a well-documented one. Propeller boss cap fins (PBCFs) – or diffusers – are readily found in shipping, but rarely in sub-24m vessels. They are widely applied, boasting 5% increases in efficiency that offer an enticing ROI. The PBCF is propulsion-source agnostic; whether it is fitted to an ICE or an electric drive, its job is to reduce noise, vibration and hub vortex.
Torqeedo’s Deep Blue 50 outboard is a rare example, as it comes with a standard five-blade, high-thrust propeller, combined with its own PBCF or HVV (hub vortex vane).