Whatever advances are achieved in terms of vessel electrification, those same ships need to charge. With shoreside infrastructure developing at a relatively slow pace, could offshore charging technology address a key need for current and future vessels? Jeff Dickson, senior engineer at Oasis Marine Power, details the technologies currently being developed and tested as the company continues to refine its offshore charging solution, which enables vessels to moor up, plug in and recharge from a zero-emission wind turbine.
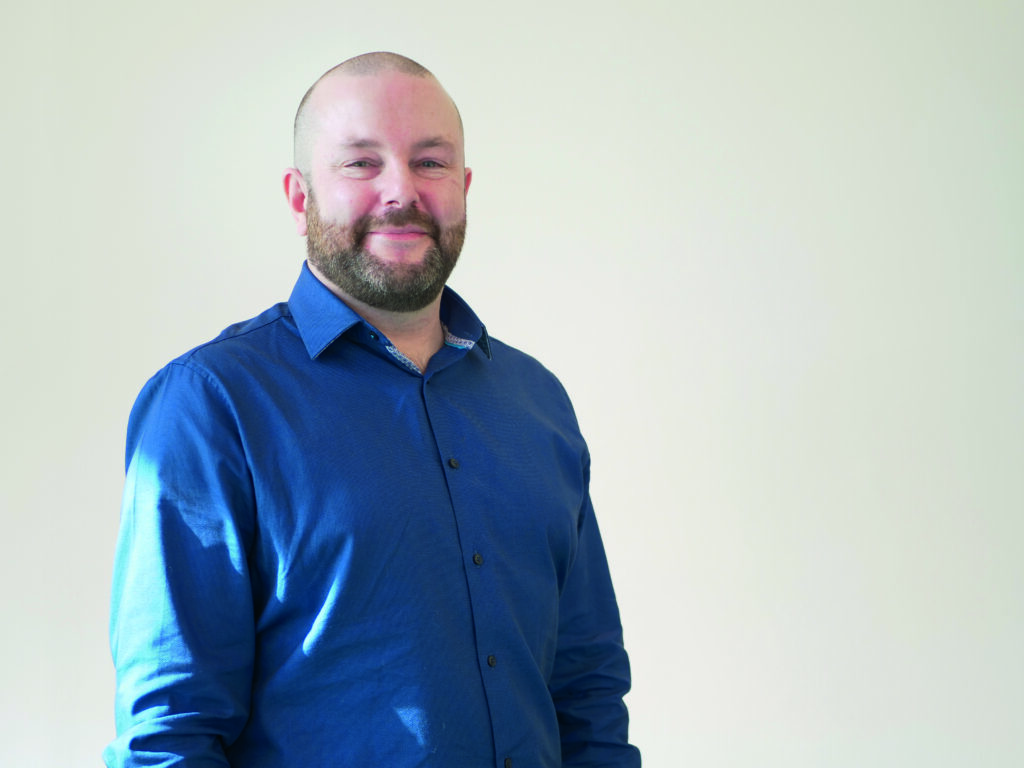
How important will offshore charging be in the development of a sustainable maritime electrification ecosystem?
Offshore charging is imperative to ensure the benefits of electrification are maximized to their full potential. Limiting charging capabilities to only within ports or harbors restricts the duration and distance electrified vessels can travel. The ability to recharge offshore will not only see a substantial reduction in CO2 emissions and fuel costs, it also fundamentally makes electric and hybrid vessels viable for offshore use. There is an industry drive to move to electrification but limited charging can be a barrier. Our current offshore charging development, the Oasis Power Buoy (OPB), will play a signification role in reducing carbon emissions for the offshore wind industry by recharging crew transfer vessels while in the field. Offshore charging will also be a key enabler for near-shore shipping. The potential is not limited to these two examples, however – as offshore charging becomes more commonplace, we would expect other shipping to make use of this technology.
Is it complementary to shoreside solutions, or are the two models mutually exclusive?
Offshore charging is complementary to shoreside charging. [When] both sources of charging use green electricity, the vessel is successfully decarbonized.
Can you tell us more about the technical details of the Oasis Power Buoy?
We are working with multiple technology options. The simplest is a ‘grid-tied’ solution where grid-level voltages are converted to DC on demand. Additionally, battery storage is an attractive option as the batteries can be trickle-charged with no large demands on the power source. Our current technology is a 2MW solution and plans are in place to develop this to greater levels as the market demands.
What safety concerns must be addressed when designing a system to be used at sea?
A core benefit of using a buoy is that vessels can moor to it safely without risk of damaging adjacent infrastructure. While moored, the vessel can shut down its propulsion, and this time can also potentially be used as rest time for the vessel’s master, thereby extending the potential working day.
On the electrical safety front, the OPB can verify the health of its subcomponents before any power is transferred. A programmable logic controller (PLC) runs tests and, to some extent, can resolve faults without human intervention. An international standard for sea charging has not yet been completed, but we fully expect to be able to meet the standard when it becomes available.
From the point of view of interaction between vessel and marine structures, the OPB system is inherently safe as it does not require direct connection between the moving vessel and the static wind turbine. Vessels will be moored at a safe distance from wind farm structures to remove any concerns about a collision between the two.
There is a real risk of mooring vessels to static structures at sea. Across the maritime world, this is avoided and mooring buoys are used. We have developed this industry best practice by integrating power transfer into the mooring buoy.
How do vessels interact with the buoy before, during and after charging?
When the vessel comes into range of the OPB, the PLCs on the buoy, vessel and wind farm will complete a series of checks to ensure the system is in good health. Charging parameters will be exchanged to ensure that the vessel’s batteries will be charged in the correct way. The power head is then transferred from the buoy and the connection is made. This connection will be sensed and checked, and charging will begin. After charging, the power head is easily returned to the buoy due to the internal mechanism.
A program of testing was undertaken at the start of 2022. What was this evaluating?
Mainly marine and mechanical testing.
What was learned, and how will this translate into further design refinements?
Minor adjustments were required to ensure the safe operation in various headings and sea states. These have now been completed.
Is there much commonality with the hydrogen buoy design?
The Oasis Hydrogen Buoy uses the same patented passive compensation design to manage the dispensing hoses – in the OPB, these are cables. Work was required to reengineer the power head and deck head for hydrogen. Working with hydrogen does necessitate different specifications from electric, but the concepts are essentially the same and did not require a complete redesign.
What’s next for the OPB development project? Is there a timeline for deployment?
The OPB will commence further sea trials shortly to complete full functional testing and further offshore reliability testing.
Image credit: Oasis Marine Power